Key Considerations for Knife Gate Valve Manufacturers Worldwide
Key Takeaways
Knife gate valves are critical components in various industrial applications, and understanding their leakage class specifications is essential for ensuring operational integrity. Manufacturers globally prioritize adherence to these standards, as they determine the reliability of the valves under pressure. The leakage class is a key performance indicator, indicating how well a knife gate valve can control fluid flow without allowing escape. High-quality manufacturers invest in rigorous testing methods to classify their valves accurately, ensuring compliance with international norms.
Prominent knife gate valve manufacturers in China have established reputations for producing durable and efficient products. They often leverage advanced manufacturing techniques and materials to achieve low leakage rates, setting benchmarks for the industry. Rigorous quality control measures are implemented during production, which include comprehensive testing to meet or exceed industry standards.
In India, the landscape of knife gate valve manufacturing is expanding rapidly. Manufacturers focus on innovation while maintaining cost-effectiveness. With an increasing emphasis on quality assurance and processing efficiency, Indian manufacturers are aligning their practices with global best practices.
Adhering to global best practices fosters trust among end-users and enhances market competitiveness for all manufacturers involved in producing knife gate valves. Overall, the integration of quality measures and adherence to leakage standards forms the cornerstone of effective knife gate valve production across different regions.
Key Factors Influencing Leakage Class in Knife Gate Valves
The leakage class of knife gate valves plays a pivotal role in determining their effectiveness across various applications. Several factors influence this classification, primarily the design and manufacturing processes adopted by knife gate valve manufacturers. First, the quality of materials used significantly impacts the valve's ability to prevent leaks. High-grade metals and corrosion-resistant alloys enhance durability while maintaining structural integrity under pressure. Second, precision in machining and assembly processes ensures tight-fitting components that reduce the likelihood of leaks over time.
Another critical aspect is the valve's design features, such as the seat configuration and sealing mechanism, which are essential for achieving optimal performance in minimizing leakage. A well-designed wafer seat or a robust elastomer sealing component can contribute to achieving higher leakage classes as defined by industry standards like ISO 5208 or ANSI/FCI 70-2.
"Investing in higher quality materials and precise manufacturing techniques can significantly elevate the reliability of knife gate valves."
Manufacturers must also contend with varying operating conditions, including temperature fluctuations and pressure changes, that could affect valve performance. Implementing stringent testing protocols prior to market release allows for the identification of potential leakage issues early in the production line.
Factor | Impact on Leakage Class |
---|---|
Material Quality | Higher resistance to wear and corrosion reduces leakage potential |
Precision Machining | Tight tolerances lead to better sealing capability |
Design Features | Superior seat designs enable effective sealing under various conditions |
Manufacturing Standards | Compliance with accepted standards ensures reliability |
By addressing these factors, knife gate valve manufacturers can enhance their product offerings while meeting or exceeding industry expectations for leak prevention, ultimately ensuring customer satisfaction and safety across applications.
Prominent Knife Gate Valve Manufacturers in China and Their Standards
The landscape of knife gate valve manufacturing in China illustrates a blend of advanced engineering practices and strict adherence to international standards. A multitude of manufacturers emphasize the significance of the leakage class specifications, which serve as critical benchmarks for assessing valve performance. Leading manufacturers such as Zhejiang Huatong Group and Shandong KAVAL, focus on producing valves that meet or exceed standards set by organizations such as the American National Standards Institute (ANSI) and the International Organization for Standardization (ISO). These companies implement rigorous testing protocols to evaluate leakage rates under various operating conditions, ensuring compliance with industry-specific requirements.
In addition to performance metrics, these manufacturers invest heavily in research and development, fostering innovation that enhances both the durability and functionality of their products. The integration of cutting-edge technology in manufacturing processes promotes efficiency while minimizing waste, aligning with global sustainability trends. Furthermore, partnerships with international suppliers contribute to the broadening of material options available for valve construction. This approach ensures that products not only meet local demands but can also compete effectively in global markets.
Compliance with established quality certifications, such as ISO 9001, remains a cornerstone for these manufacturers. Regular audits and continuous training programs for personnel underscore their commitment to maintaining high-quality standards throughout production stages. The focus on these quality measures not only assures product reliability but also reinforces consumer trust in their knife gate valves, establishing a reputation that extends beyond China's borders.
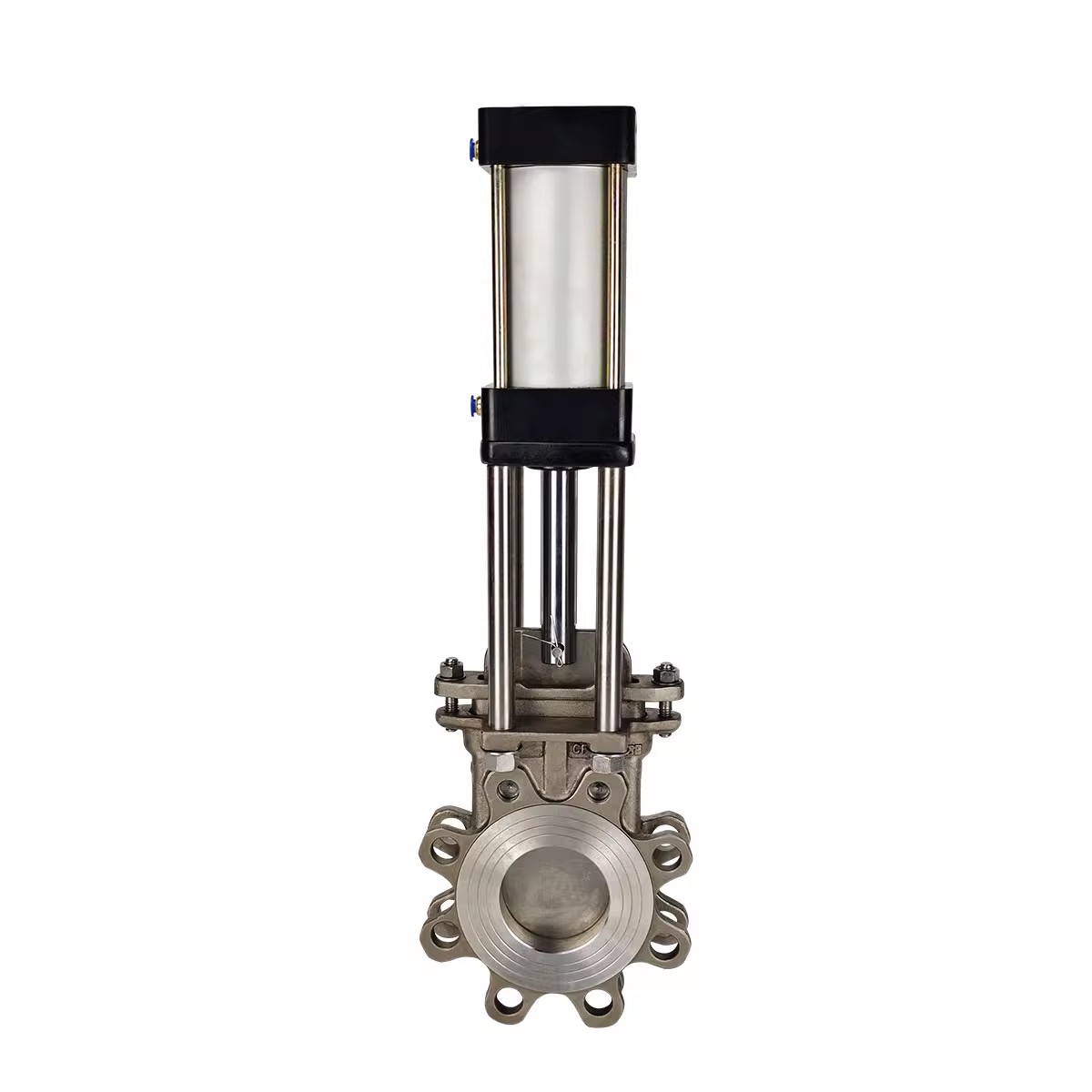
Overview of Knife Gate Valve Production Practices in India
The production practices for knife gate valves in India are shaped by a combination of technological advancements, skilled labor, and stringent industry standards. Manufacturers focus on optimizing their processes to enhance efficiency and product quality. Key aspects include the use of advanced materials that can withstand high pressure and challenging conditions. This choice of materials is crucial for achieving high leakage class ratings, which directly influence the performance and reliability of the valves. Factory settings often employ precision machining techniques to ensure tight tolerances in valve dimensions.
The adoption of automation technologies has gained momentum, allowing for consistent part quality and reduced labor costs. Manufacturers also prioritize thorough quality control at each stage of production, including detailed inspections to assess valve integrity and functionality. Testing protocols are implemented to evaluate performance under various conditions, thus helping ensure compliance with international standards.
Collaboration with experienced engineers plays a vital role in refining production practices, offering insights into optimizing operational workflows. As global demand grows for high-quality knife gate valves, Indian manufacturers continue to innovate, balancing cost-effectiveness with superior craftsmanship. This approach positions them competitively in both local and international markets while maintaining their commitment to excellence in the valve manufacturing sector.
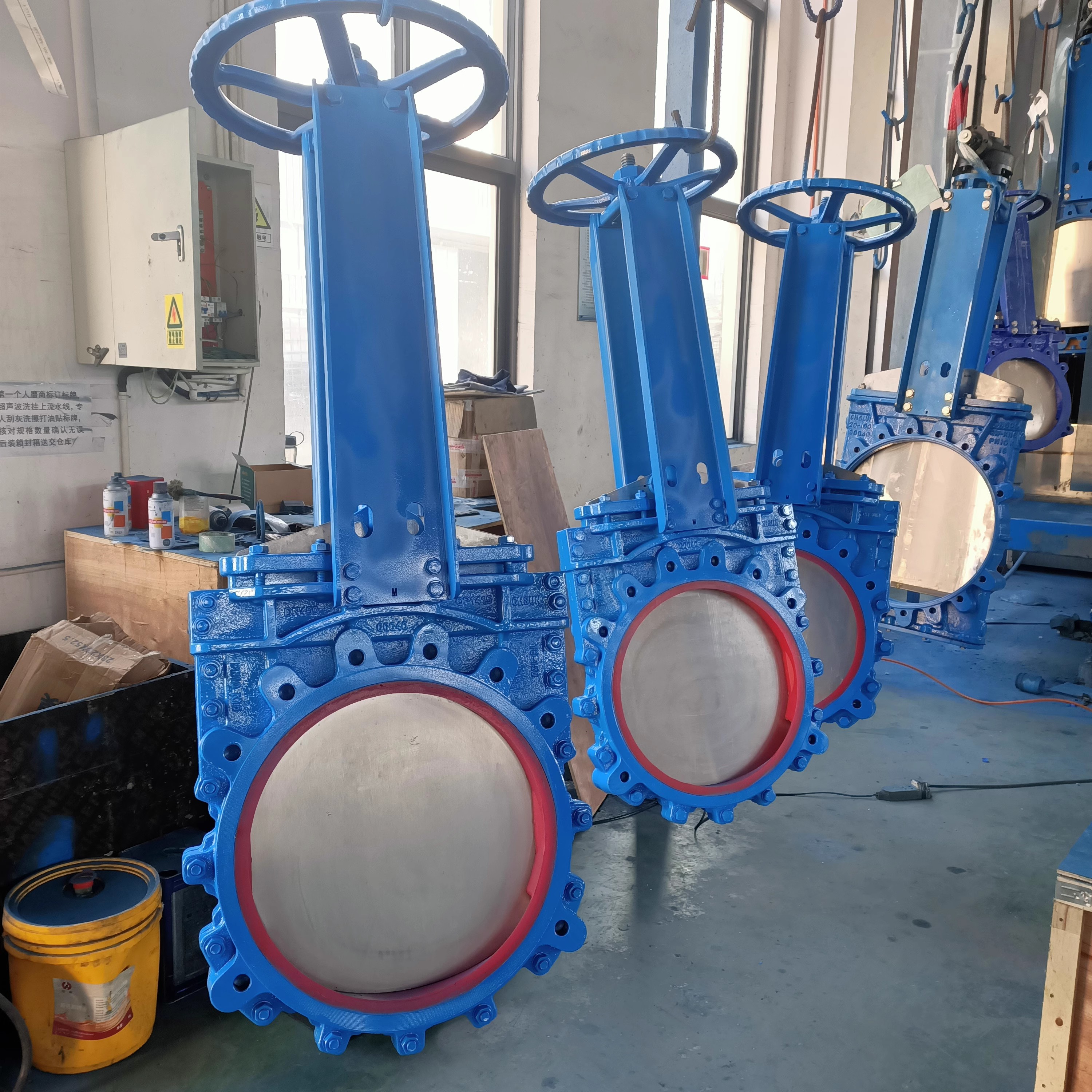
Global Best Practices for Ensuring Quality in Knife Gate Valves
Maintaining high-quality standards in knife gate valves involves adherence to rigorous manufacturing practices and leakage class specifications. Manufacturers prioritize material selection, often opting for durable alloys and polymers, which significantly enhance the valves' longevity and operational reliability. Detailed inspection protocols are mandated at various stages of production, ensuring that any potential quality issues are identified and addressed promptly. Additionally, adherence to international standards such as API, ANSI, and ISO is critical in the design and testing processes, providing a framework for performance metrics that uphold safety and efficiency. The deployment of advanced testing technologies, including hydrostatic and pneumatic tests, further affirms the integrity of each valve produced. Companies in China and India, prominent players in the industry, have embraced these best practices to ensure their products not only meet but exceed global expectations. Continuous training programs for engineers and technicians facilitate up-to-date knowledge of emerging technologies and trends, reinforcing quality control efforts throughout the manufacturing process. This structured approach allows manufacturers to deliver reliable products that perform effectively under varied operational conditions.
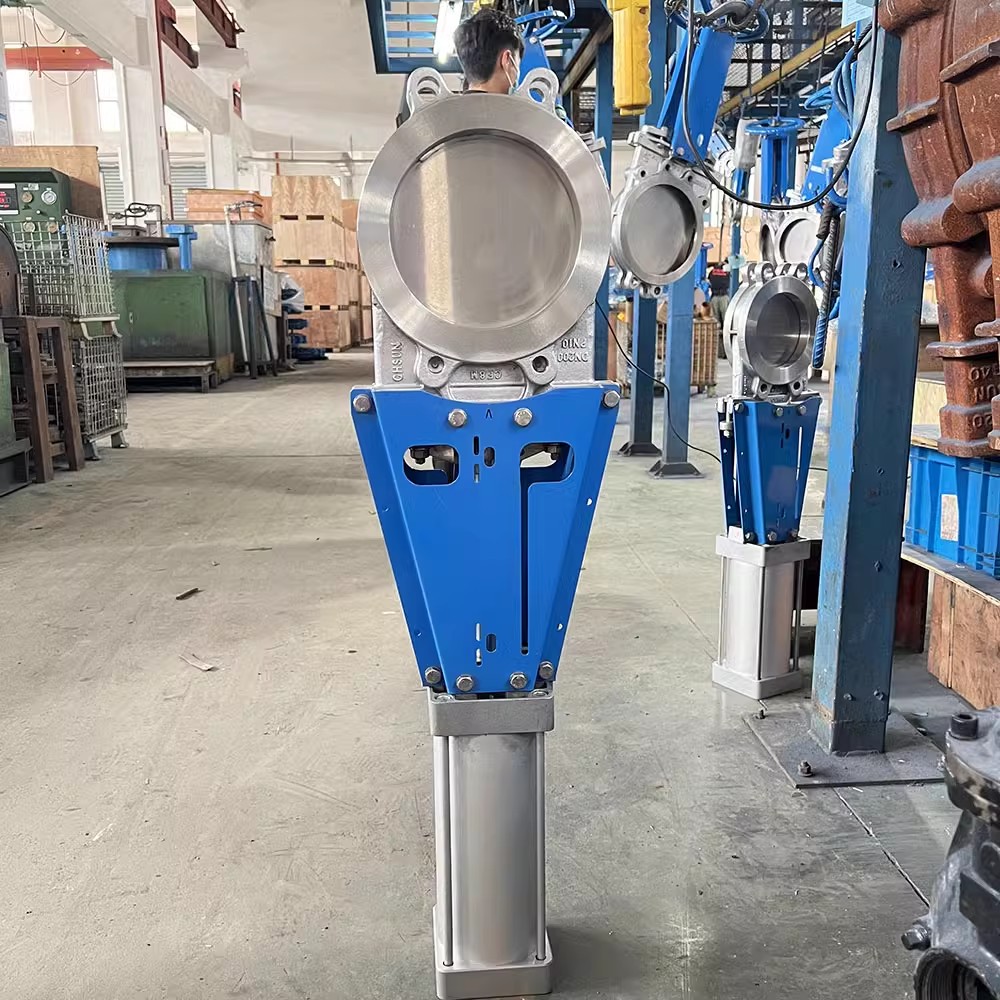
Conclusion
The landscape of knife gate valve manufacturing showcases a diverse range of players committed to meeting industry needs. Key factors influencing leakage class specifications hold significant importance for manufacturers as they navigate the competitive market. In regions such as China and India, leading manufacturers have adopted stringent standards that govern production practices to elevate the quality of their offerings. Industry stakeholders recognize that ensuring compliance with established standards enhances product reliability and customer trust. Continuous improvement within manufacturing processes, alongside adherence to quality assurance protocols, underscores the responsibility manufacturers bear in delivering effective solutions. The establishment of global best practices can further streamline operations, paving the way for innovations that enhance performance while maintaining safety and efficiency. The dedication to quality and reliability remains paramount in solidifying a manufacturer's reputation in this ever-evolving sector.
FAQs
What is the leakage class for knife gate valves?
Leakage class indicates the allowable leakage rate of a knife gate valve under specific conditions. It is an essential factor in determining the valve's performance and suitability for different applications.
Why is the leakage class important for knife gate valves?
The leakage class helps industry professionals select valves that meet safety and operational requirements. A lower leakage class value signifies tighter sealing, minimizing the risk of fluid loss or contamination.
Who are the leading knife gate valve manufacturers in China?
Several prominent manufacturers in China specialize in knife gate valves. These companies focus on innovation, quality control, and compliance with international standards.
How do Indian manufacturers compare with their Chinese counterparts?
Indian manufacturers often prioritize cost-effectiveness and materials innovation. Despite differences in pricing structures, many Indian producers maintain high quality while competing globally.
What production practices ensure quality in knife gate valves?
Quality assurance practices include stringent testing procedures, adherence to industry certifications, and integration of modern manufacturing technologies to enhance reliability and performance.
What industry standards should knife gate valve manufacturers follow?
Manufacturers should comply with standards such as ISO, API, ASME, and other global regulations to ensure their products meet safety and performance benchmarks.
How can buyers verify the reliability of a knife gate valve manufacturer?
Buyers can assess manufacturer reliability through reviews, certifications, and references from previous clients. Analyzing production capacity and technology capabilities also provides insights into potential partnerships.
Are there specific certifications that reputable knife gate valve manufacturers hold?
Yes, reputable manufacturers often hold certifications like ISO 9001 for quality management systems and other relevant industry-specific certifications that demonstrate compliance with global standards.