Exploring Knife Type Gate Valve Options: Lever Lined and Lug Variants
Key Takeaways
Exploring the various knife type gate valve options reveals distinct characteristics and efficiencies tailored for specific industrial applications. The lever operated knife gate valve stands out with its ergonomic design, allowing for smoother operation and quick adjustments during processes. This type is particularly suitable for situations requiring frequent use, as the lever mechanism minimizes operator fatigue while maximizing control precision. Similarly, lined knife gate valves offer an additional layer of protection through their special coatings that resist corrosion and erosion, making them ideal for handling abrasive and corrosive media. These valves enhance longevity and reliability in demanding environments. Furthermore, the lug type knife gate valve and lug knife gate valve variants provide flexibility in installation thanks to their unique mounting options, allowing seamless integration into existing piping systems without the need for additional support structures. Their design is advantageous in applications where space is limited or where disassembly is necessary for maintenance. As industries continue to prioritize efficiency and safety, understanding these unique features aids in selecting the appropriate valve type for specific operational needs.
Overview of Knife Type Gate Valve Variants
Knife type gate valves are essential components in various industrial applications, providing efficient fluid control and isolation. These valves are designed to handle slurries, viscous fluids, and other challenging substances. The lever operated knife gate valve features a straightforward design that allows for quick operation and reliable sealing; operators can easily manage flow with minimal physical effort. In contrast, lined knife gate valves offer enhanced corrosion resistance, making them ideal for handling aggressive chemicals. The lining materials protect the valve body from degradation, thereby extending the valve's lifespan.
The lug knife gate valve variant employs a unique fastening system that allows for easy installation and maintenance without needing additional support. This design enables users to remove the valve from the pipeline without disturbing adjacent components, simplifying repairs or replacements. Each variant presents distinct advantages tailored to specific operational demands.
Choosing the right type of knife gate valve is crucial in optimizing system performance while ensuring safety and reliability. Understanding these variants aids operators in selecting the appropriate valve for their specific fluid control needs.
"Selecting the right knife type gate valve can significantly impact system efficiency and reliability."
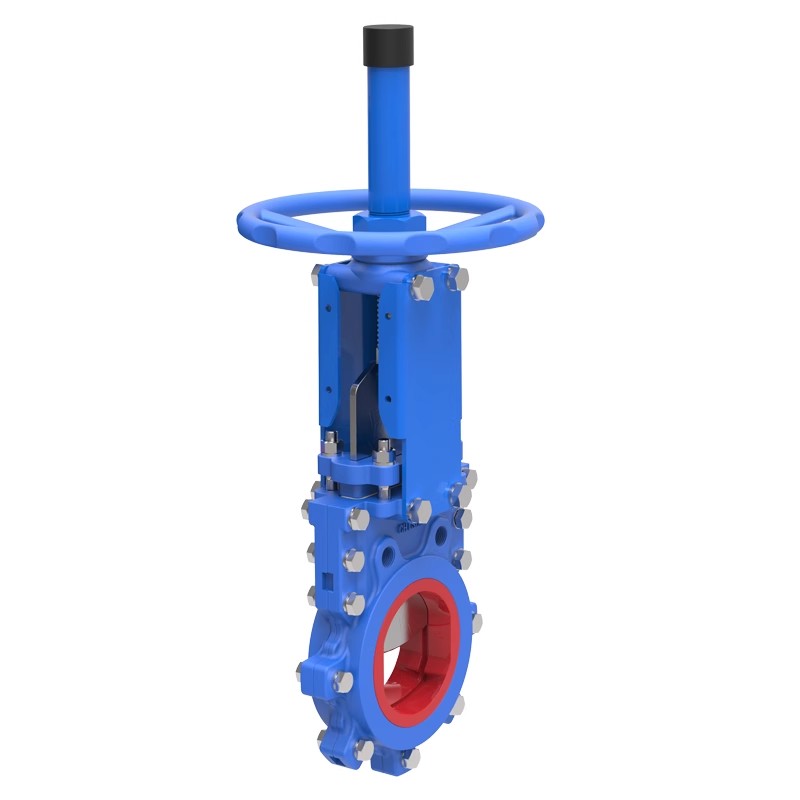
Unique Features of Lever Operated Knife Gate Valves
Lever operated knife gate valves distinguish themselves through their simplicity, durability, and effective performance in various fluid control applications. The lever mechanism provides an intuitive operation that enables swift valve actuation, which is vital in industrial processes requiring precise control over liquid or gas flow. This type of valve typically features a flat blade design that slices through the medium, effectively minimizing flow resistance and providing a tight seal when closed.
One notable advantage is the ease of maintenance. The construction allows for quick disassembly and repair, reducing downtime during maintenance activities. Operators can easily replace the sealing elements without needing extensive tools or specialist training. The use of robust materials in the design ensures that these valves can withstand harsh operating conditions, including high pressure and corrosive environments.
Another important feature is their versatility in application. Lever operated knife gate valves are particularly suited for industries handling slurries, solids, or viscous fluids due to their ability to handle high particulate content without malfunctioning. Their robust construction accommodates a range of operating temperatures and pressures, making them adaptable to specific operational requirements.
The table below summarizes the key features of lever operated knife gate valves:
Feature | Description |
---|---|
Operation Mechanism | Manual lever actuation |
Maintenance | Easy disassembly for repair |
Construction Material | Durable materials designed for harsh conditions |
Flow Characteristics | Minimal flow resistance with a tight seal |
Versatility | Suitable for slurries, solids, and viscous fluids |
Lever operated knife gate valves play a critical role in enhancing efficiency across multiple sectors while ensuring reliability and ease of use in demanding environments. Their unique attributes reinforce their position as essential components for effective fluid management systems.

Benefits and Applications of Lined Knife Gate Valves
Lined knife gate valves offer significant advantages in environments where corrosion resistance is crucial. The internal lining of these valves often consists of materials such as PTFE or rubber, which provide enhanced durability against aggressive chemicals and abrasive slurries. Utilizing lined models minimizes wear and extends the valve's lifespan, ensuring reliable performance in harsh conditions.
Applications for lined knife gate valves span various industries, including wastewater treatment, mining, and chemical processing. In these sectors, the need for effective sealing while managing viscous or particulate-laden fluids is critical. The design allows for full port flow, which reduces turbulence and pressure drop, promoting efficient fluid transfer.
Installation benefits also contribute to their popularity. Lined knife gate valves can be integrated into existing systems seamlessly due to their versatile design. Their compact footprint enables easy handling without requiring extensive modifications to piping setups. Maintenance is simplified; the ability to replace the lining if wear occurs can significantly reduce costs compared to replacing the entire valve.
Overall, lined knife gate valves stand out for their reliability, cost-effectiveness, and long-term performance, making them a preferred choice in settings demanding high operational standards.
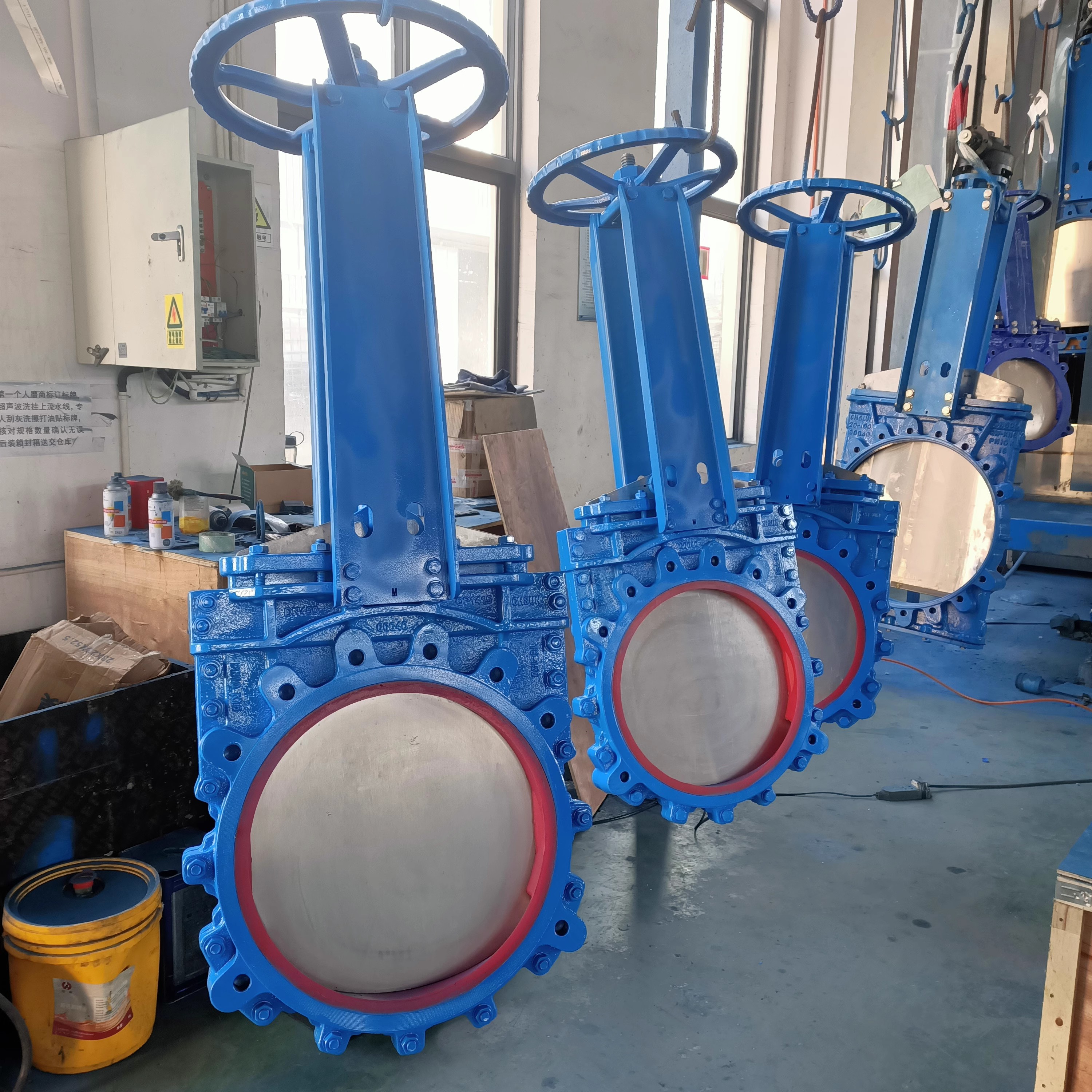
Understanding Lug Type and Lug Knife Gate Valves
Lug type knife gate valves are engineered for reliability and ease of installation in various industrial applications. The unique design features threaded lugs on the valve body, allowing for secure attachment to pipelines without the need for additional support brackets. This capability facilitates the installation process, particularly in restricted spaces. The operation of a lug knife gate valve is characterized by its ability to provide tight sealing, effectively preventing leakage when the valve is closed. This is crucial in systems where maintaining fluid integrity is a priority. Often made from robust materials like stainless steel or cast iron, lug type knife gate valves are suitable for handling abrasive materials, making them ideal for wastewater treatment, mining, and other demanding environments. Their versatility extends to applications involving both liquid and dry media, thus broadening their usability across various sectors. Proper selection of these valves can significantly enhance both operational efficiency and system reliability, contributing to longer service life and reduced maintenance costs.
Conclusion
Knife type gate valves play a crucial role in industrial fluid control, with various designs catering to specific operational needs. The lever operated knife gate valve offers easy operation and efficient sealing, making it suitable for applications where minimal leakage is essential. In contrast, lined knife gate valves provide an added layer of protection against corrosive materials, ensuring longevity and reliability in harsh environments. The lug type knife gate valve features threaded connections that facilitate installation and maintenance, a significant advantage for systems that require flexibility and adaptability. Each variant possesses distinct characteristics tailored to diverse industries. Selecting the appropriate knife type valve depends on factors such as the nature of the fluid, pressure requirements, and installation space constraints. Understanding these options allows engineers and decision-makers to optimize their systems for enhanced performance and safety.
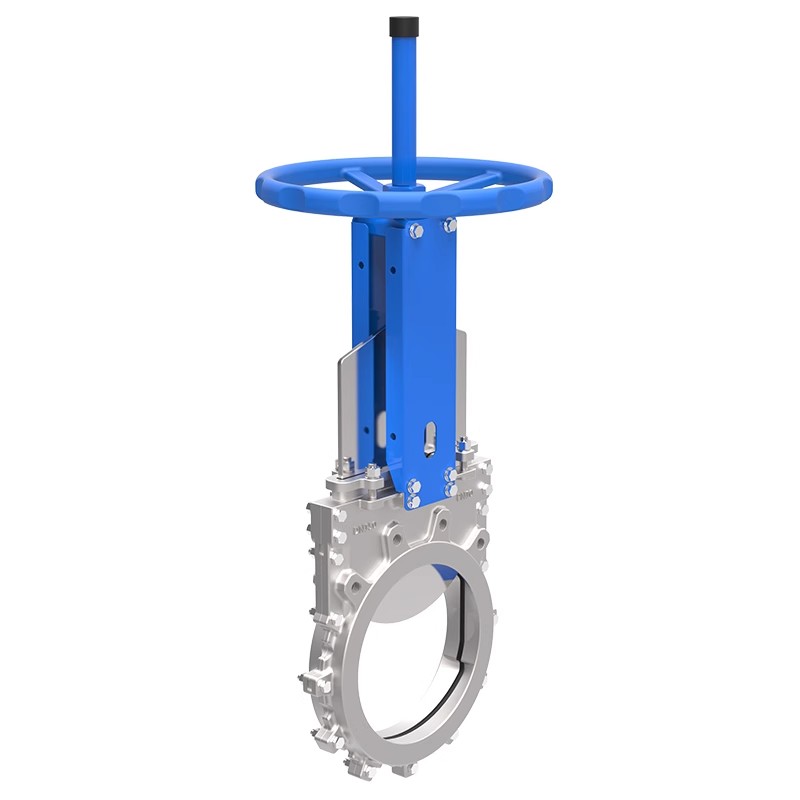
FAQs
What is a knife type gate valve?
A knife type gate valve is a specialized valve designed to control the flow of fluids in various industrial applications. Its unique blade-like structure enables it to cut through tough materials, making it effective for slurries and viscous media.
How does a lever operated knife gate valve function?
A lever operated knife gate valve uses a mechanical lever to open or close the valve. The lever allows for quick operation and control over the flow, providing an efficient solution for environments where manual control is necessary.
What are the advantages of using lined knife gate valves?
Lined knife gate valves feature protective linings that enhance durability and resistance to corrosion. These linings help maintain the integrity of the valve when handling abrasive or chemically aggressive substances, making them suitable for demanding applications.
What differentiates **lug knife gate valves* from other types?
**Lug knife gate valves* are equipped with lugs that facilitate easy installation and maintenance. This design allows for mounting between two flanges without requiring additional hardware, streamlining installation processes in various pipeline systems.
In which industries are knife type gate valves commonly used?
Knife type gate valves find application in industries such as wastewater treatment, pulp and paper, mining, and chemical processing. Their robust design makes them ideal for handling challenging materials like slurries, sludge, and other viscous fluids.
How can users ensure proper maintenance of their knife type gate valves*?
Regular maintenance includes inspecting seals and gaskets for wear, ensuring the operational mechanism remains lubricated, and checking for any debris accumulation around the blade. These practices help maintain optimal functionality over time.