Application | General | Place of Origin | Shenzhen, China |
---|
Power | Electric | Customized support | OEM |
---|
Warranty | 1 year | Model Number | DZ973H-6 DZ973H-10 DZ973H-16 |
---|
Temperature of Media | Normal Temperature | Brand Name | Freya |
---|
Media | Gas | Input signal | 4~20mA |
---|
Output signal | 4~20mA | Valve Body Material | WCB WC6/WC9 |
---|
Bonnet Material | WCB 12Cr1MoV | Valve Rod Material | 38CrMoAlA 25Cr2MoV |
---|
Flashboard Material | 25/WCB WC6/WC9 | Universal Joint Material | 38CrMoAlA 38CrMoAlA |
---|
Bolt Material | B7 25Cr2MoV | Applicable Medium Material | Water, Gas, Oil, etc. |
1. Introduction
The DZ973H series Remote Control Motorized Stem Knife Gate Valves are designed for precise and automated control of fluid flow in various industrial applications. These valves feature a robust knife gate design and a motorized stem for efficient and reliable remote operation. The series includes DZ973H-6, DZ973H-10, and DZ973H-16 models, each suitable for different pressure ratings.
2. Features
- Material: Stainless Steel body and gate (SS304/SS316).
- Design: Knife gate design to handle slurry, viscous, and abrasive fluids.
- Seal: Resilient or metal-to-metal seal options for tight closure.
- Actuation: Motorized stem for remote control operation.
- Connection: Flanged, wafer, or lugged ends for versatile installation.
- Pressure Rating: PN6 (6 bar), PN10 (10 bar), PN16 (16 bar).
- Standards: Manufactured according to industry standards (e.g., ISO, API).
3. Applications
- Mining industry.
- Wastewater treatment plants.
- Pulp and paper industry.
- Chemical processing.
- Power generation.
4. Technical Specifications
Parameter | Specification |
---|
Valve Size | Various sizes available |
Body Material | Stainless Steel (SS304/SS316) |
Gate Material | Stainless Steel (SS304/SS316) |
Seal Material | Resilient (EPDM, NBR, etc.) or Metal-to-Metal |
Pressure Rating | PN6 (DZ973H-6), PN10 (DZ973H-10), PN16 (DZ973H-16) |
Temperature Range | -10°C to 200°C (14°F to 392°F) |
Connection Type | Flanged, Wafer, Lugged |
Face-to-Face Dimension | According to ISO 5752 or API 609 |
Media | Slurry, abrasive and viscous fluids |
Operating Voltage | Typically 220V/380V AC |
Actuation | Motorized Stem |
Leakage Rate | Zero leakage (resilient seal) |
Testing Standard | API 598 |
5. Installation Instructions
5.1 Preparation
- Ensure the pipeline is clean and free of debris.
- Verify that the valve specifications match the application requirements.
- Check the motorized stem for proper configuration and voltage compatibility.
5.2 Alignment
- Align the valve with the pipeline flanges.
- Ensure proper alignment to avoid stress on the valve body and flanges.
5.3 Bolting
- Secure the valve using appropriate bolts and nuts.
- Tighten bolts evenly in a crisscross pattern to ensure a proper seal.
5.4 Electrical Connection
- Connect the motorized stem to the power supply according to the manufacturer's wiring diagram.
- Ensure all electrical connections are secure and properly insulated.
5.5 Testing
- Test the valve for proper operation using the motorized stem.
- Check for leaks and ensure the valve opens and closes smoothly.
6. Maintenance
6.1 Regular Inspection
- Periodically inspect the valve and motorized stem for signs of wear or damage.
- Check the gate, seals, and stem for any abnormalities.
6.2 Seal Replacement
- Replace the seals if leakage is detected.
- Use compatible seal materials for the specific media and operating conditions.
6.3 Motorized Stem Maintenance
- Follow the motorized stem manufacturer's maintenance guidelines.
- Ensure the motorized stem operates smoothly and is free from debris.
6.4 Gate Inspection
- Inspect the gate for wear and replace if necessary.
- Ensure the gate moves freely without obstruction.
7. Safety Precautions
- Ensure the pipeline is depressurized before performing any maintenance.
- Use appropriate personal protective equipment (PPE) when handling the valve.
- Follow all relevant safety standards and guidelines.
- Ensure all electrical connections are de-energized before maintenance.
8. Troubleshooting
Issue | Possible Cause | Solution |
---|
Valve does not open/close | Obstruction in the gate area | Inspect and clean the gate area |
Leakage through the seal | Worn or damaged seal | Replace the seal |
Motorized stem not responding | Electrical issue or actuator fault | Check electrical connections and motorized stem status |
Difficulty in manual operation | Debris or damage in the stem or gate | Clean and inspect the stem and gate |
Product Show
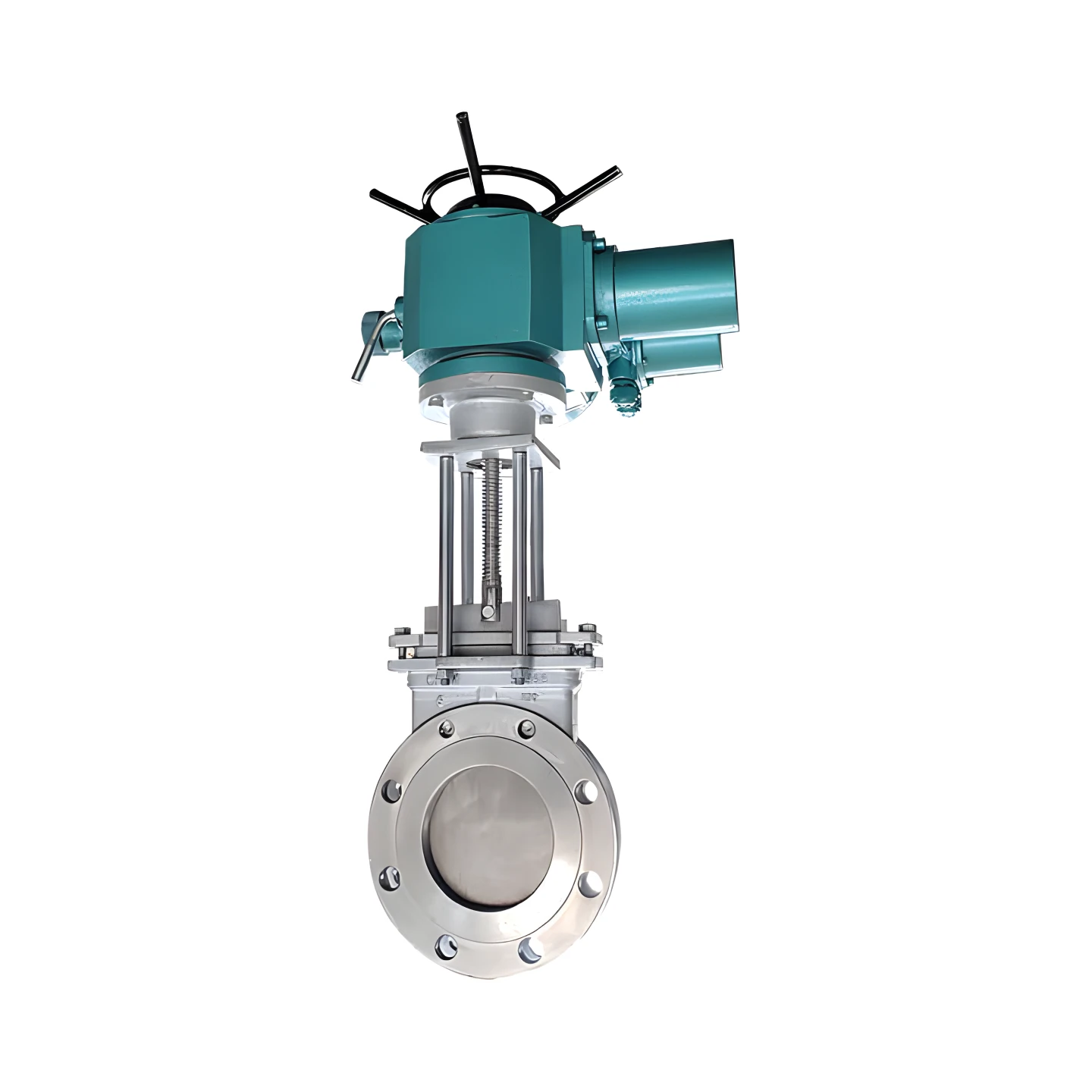
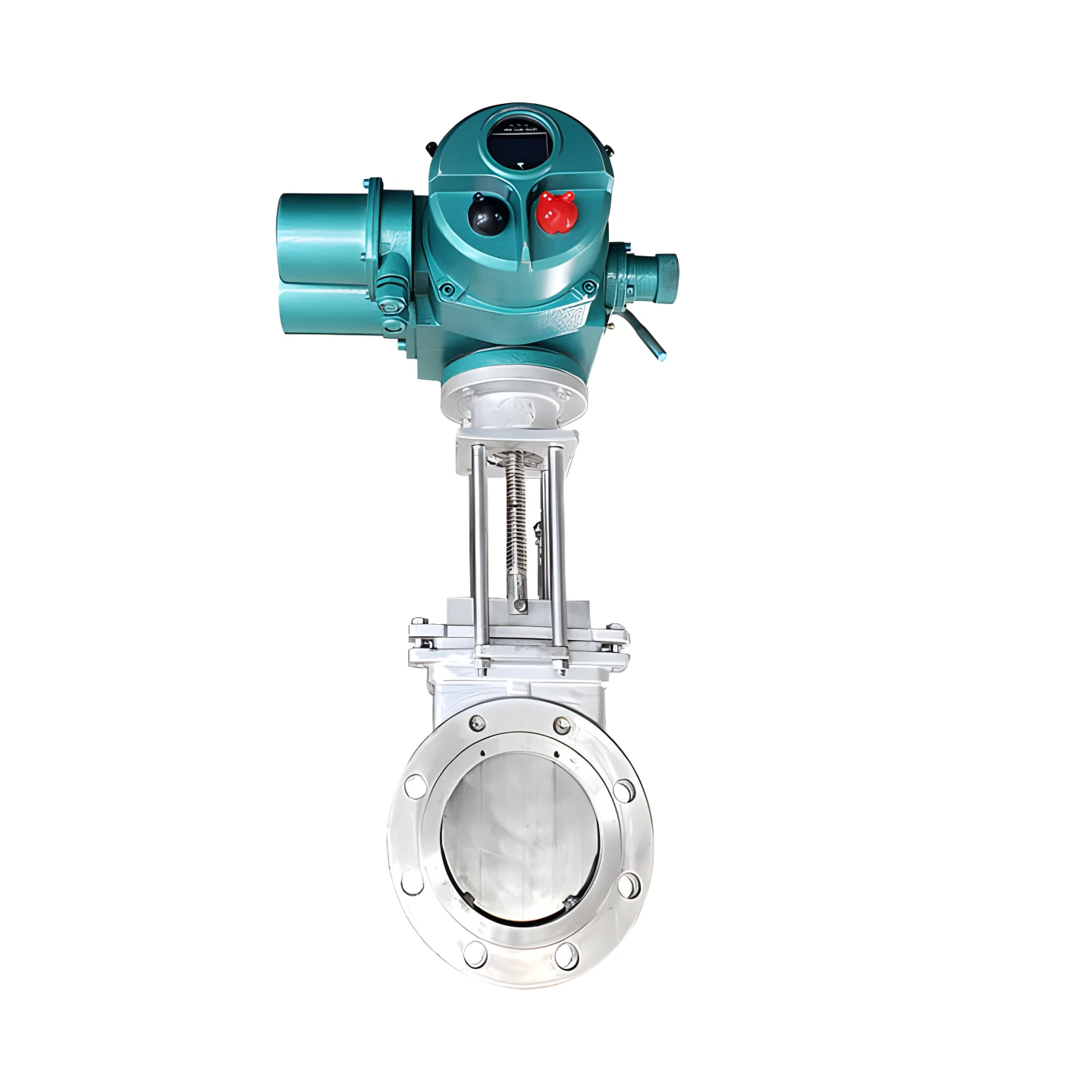
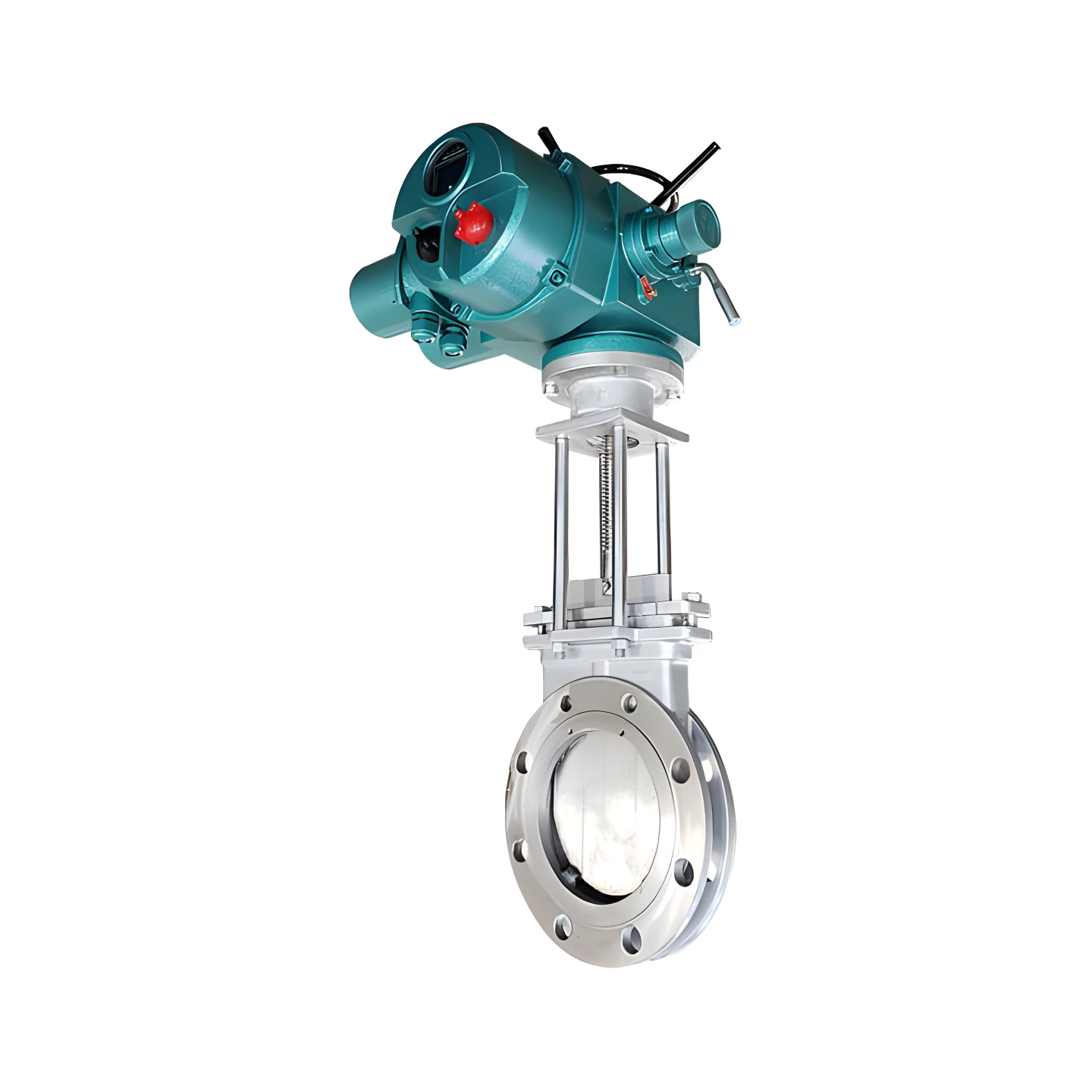
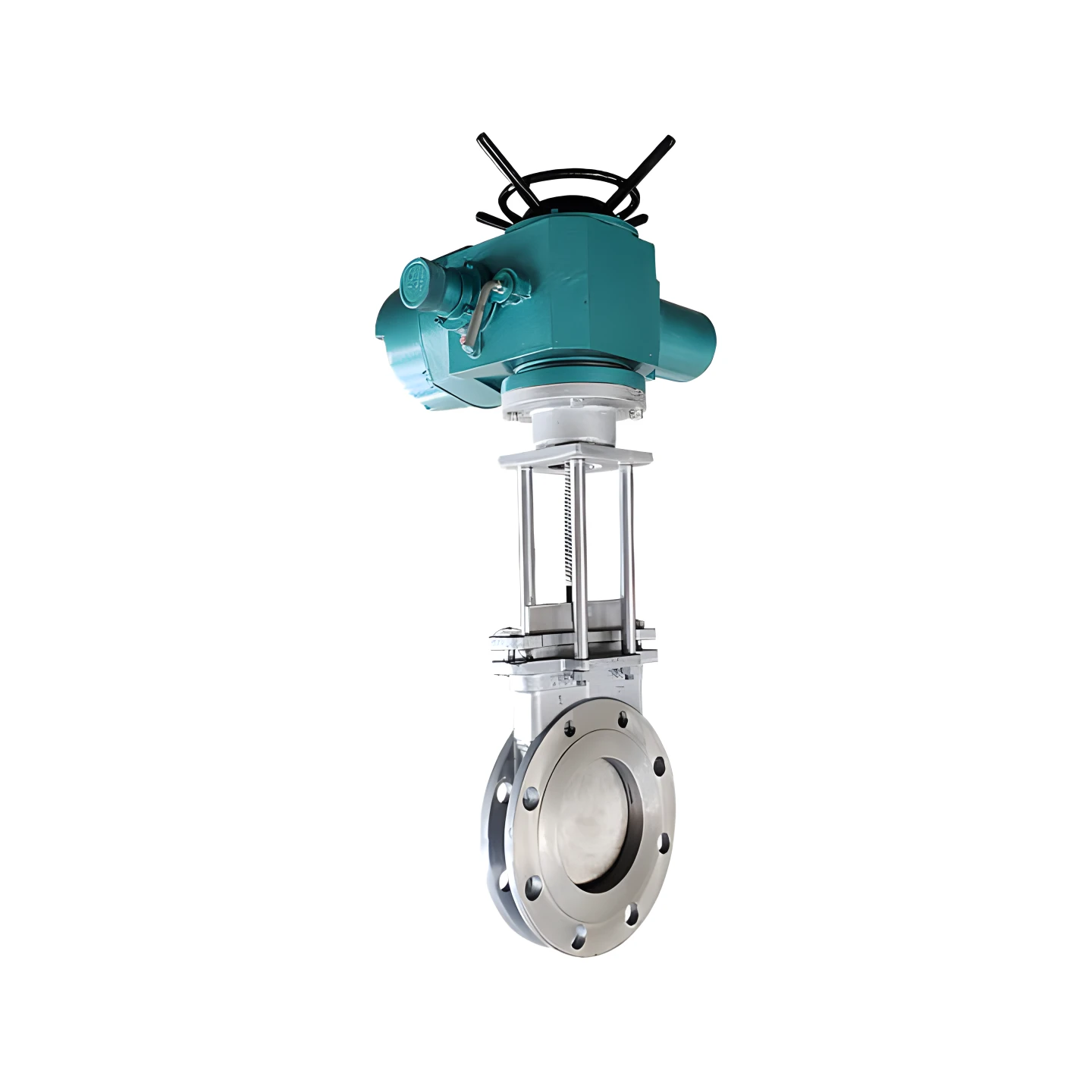
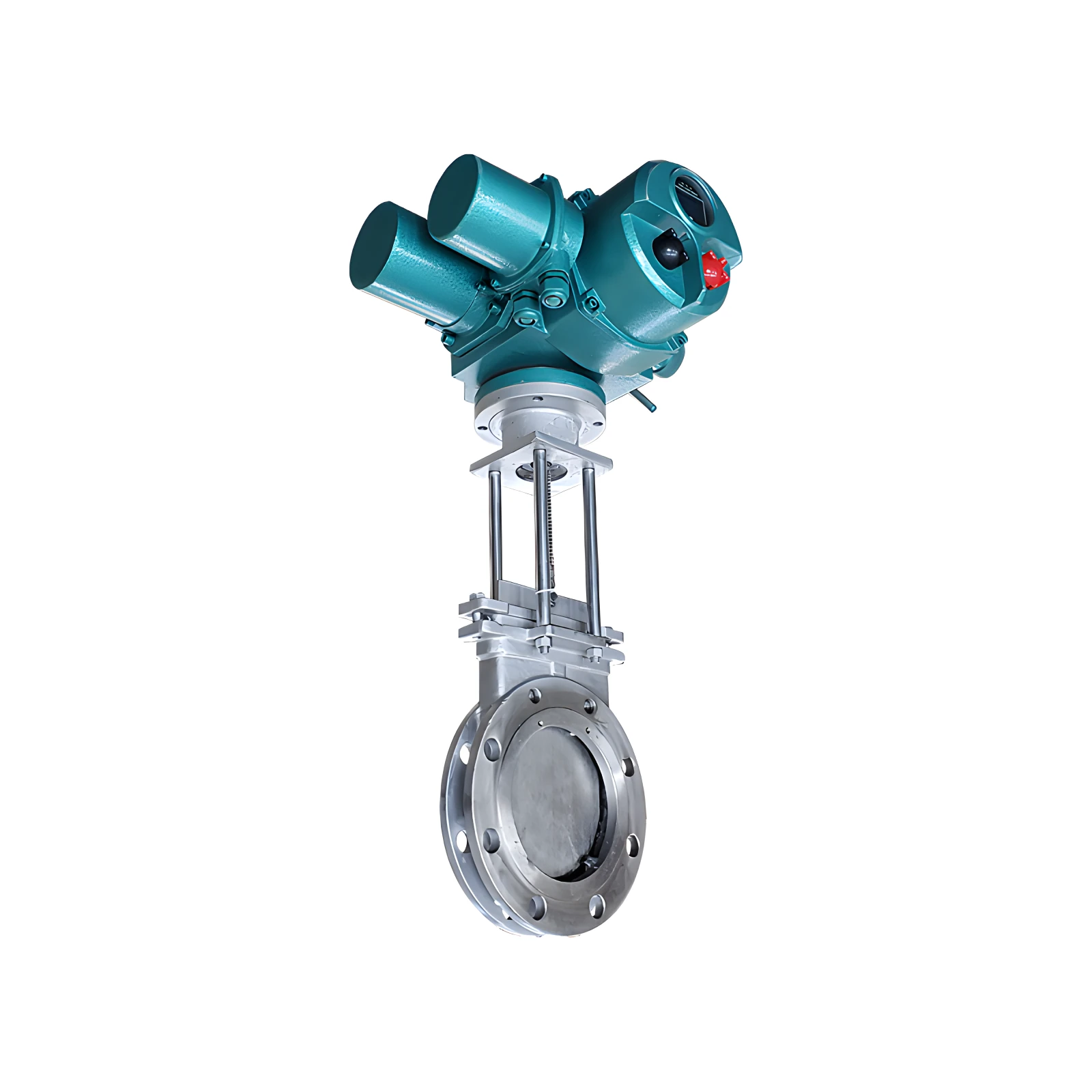