Application | General | Place of Origin | Shenzhen, China |
---|
Power | Manual | Customized support | OEM, ODM, OBM, Software reengineering |
---|
Warranty | 2 years | Model Number | PZ73TC |
---|
Temperature of Media | Medium Temperature, Normal Temperature | Brand Name | SHANGCHENG |
---|
Media | Water | product name | Ceramic knife gate valve |
---|
Working pressure | 1.0-1.6Mpa (10-25bar) | Stem | 2cr13 |
---|
Body material | Cast steel and stainless steel | Valve plate material | Ceramic |
---|
sealing material | Ceramic | temperature | -45-130℃ |
---|
Working medium | Sewage, pulp, etc | Connection type | clamp valves |
---|
operation | Hand wheel, pneumatic, electric | | |
1. Introduction
The Cast Steel Stainless Steel Ceramic Knife Gate Valve is designed for highly abrasive and corrosive applications. The integration of ceramic components provides exceptional wear resistance, making it ideal for industries such as mining, power generation, and chemical processing where handling slurries and other abrasive media is common.
2. Features
- Material: Cast steel body with stainless steel trim and ceramic inserts for enhanced durability and wear resistance.
- Design: Knife gate design to cut through thick and abrasive media, ensuring smooth flow and minimal clogging.
- Seal: Resilient seal providing tight closure and preventing leakage.
- Actuation: Available in manual, pneumatic, or electric actuation options.
- Connection: Flanged ends for easy installation and secure connection.
- Pressure Rating: Suitable for medium to high-pressure applications.
- Ceramic Inserts: High-quality ceramic inserts in the gate and seat areas for maximum wear resistance.
3. Applications
- Mining industry.
- Power generation.
- Chemical processing.
- Pulp and paper industry.
- Wastewater treatment plants.
4. Technical Specifications
Parameter | Specification |
---|
Valve Size | Various sizes available |
Body Material | Cast Steel (WCB) |
Gate Material | Stainless Steel (SS304/SS316) with Ceramic Inserts |
Seal Material | Resilient (EPDM, NBR, etc.) |
Pressure Rating | PN10, PN16, or higher |
Temperature Range | -10°C to 200°C (14°F to 392°F) |
Connection Type | Flanged |
Face-to-Face Dimension | According to ISO 5752 |
Media | Slurry, abrasive and corrosive fluids |
Operating Pressure | 1.0 MPa (PN10) or higher |
Actuation | Manual, Pneumatic, Electric |
Air Supply Pressure (Pneumatic) | 0.4 - 0.7 MPa |
Leakage Rate | Zero leakage (resilient seal) |
Testing Standard | API 598 |
5. Installation Instructions
- Preparation: Ensure the pipeline is clean and free of debris.
- Alignment: Align the valve with the pipeline flanges.
- Bolting: Secure the valve using appropriate bolts and nuts, ensuring even tightening.
- Actuation Connection:
- For pneumatic actuators, connect the actuator to the air supply according to the manufacturer’s instructions.
- For electric actuators, ensure proper electrical connections are made.
- Testing: Test the valve for proper operation and check for leaks.
6. Maintenance
- Regular Inspection: Periodically inspect the valve and actuator for signs of wear or damage.
- Seal Replacement: Replace the seals if leakage is detected.
- Stem Maintenance: Ensure the stem operates smoothly and is free from debris.
- Actuator Maintenance: Follow the actuator manufacturer’s maintenance guidelines.
- Ceramic Insert Inspection: Regularly inspect the ceramic inserts for signs of wear or damage and replace if necessary.
7. Safety Precautions
- Ensure the air supply or electrical power is disconnected before performing any maintenance.
- Use appropriate personal protective equipment (PPE) when handling the valve.
- Follow all relevant safety standards and guidelines.
8. Troubleshooting
Issue | Possible Cause | Solution |
---|
Valve does not open/close | Obstruction in the gate area | Inspect and clean the gate area |
Leakage through the seal | Worn or damaged seal | Replace the seal |
Actuator malfunction | Air supply issue or actuator failure | Check air supply and inspect the actuator (for pneumatic) or check electrical connections (for electric) |
Wear on ceramic inserts | High abrasion or impact | Replace the ceramic inserts |
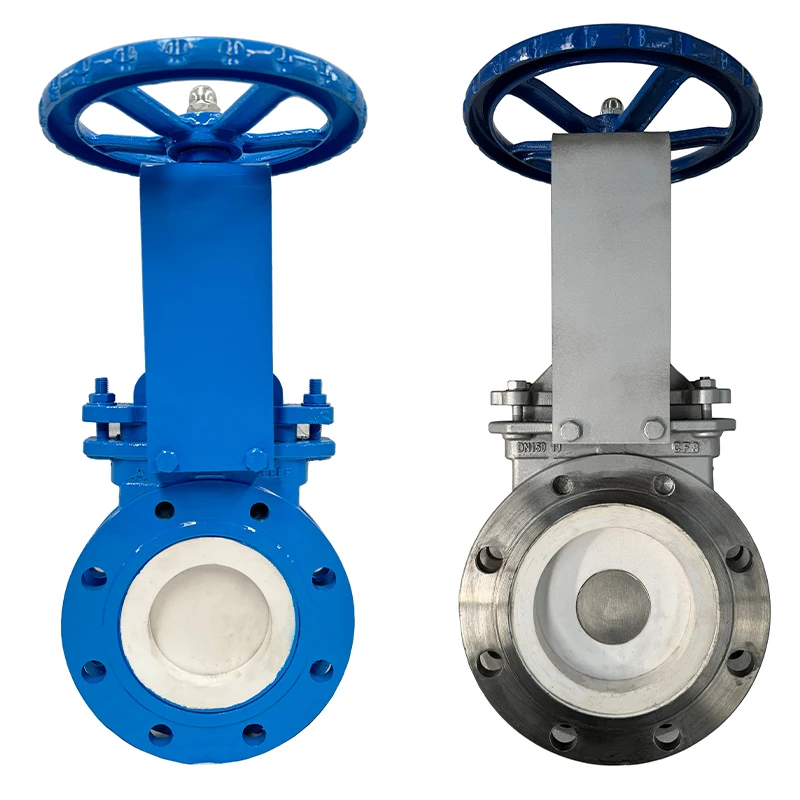
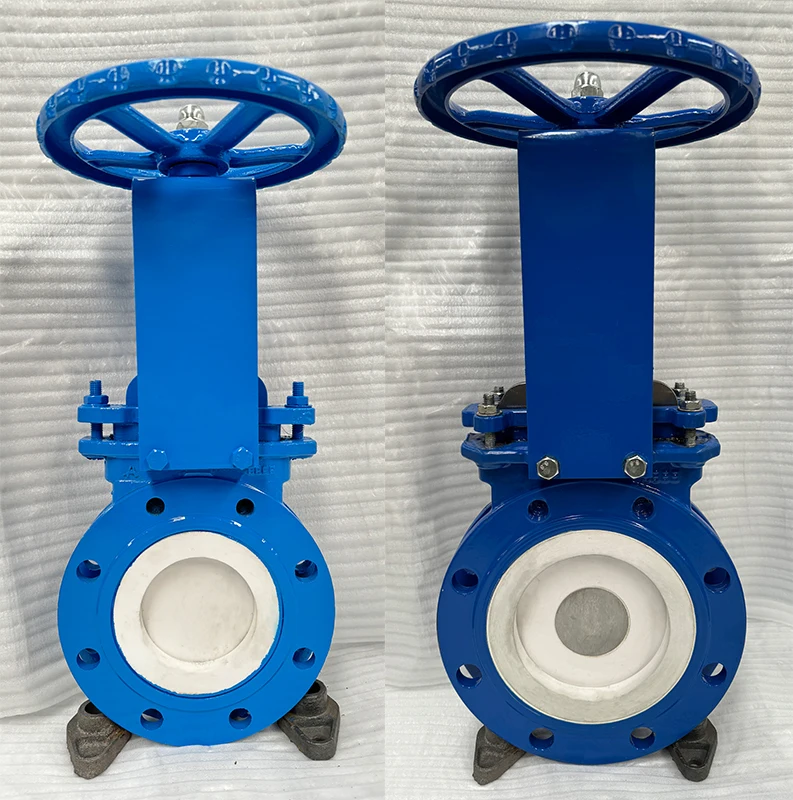
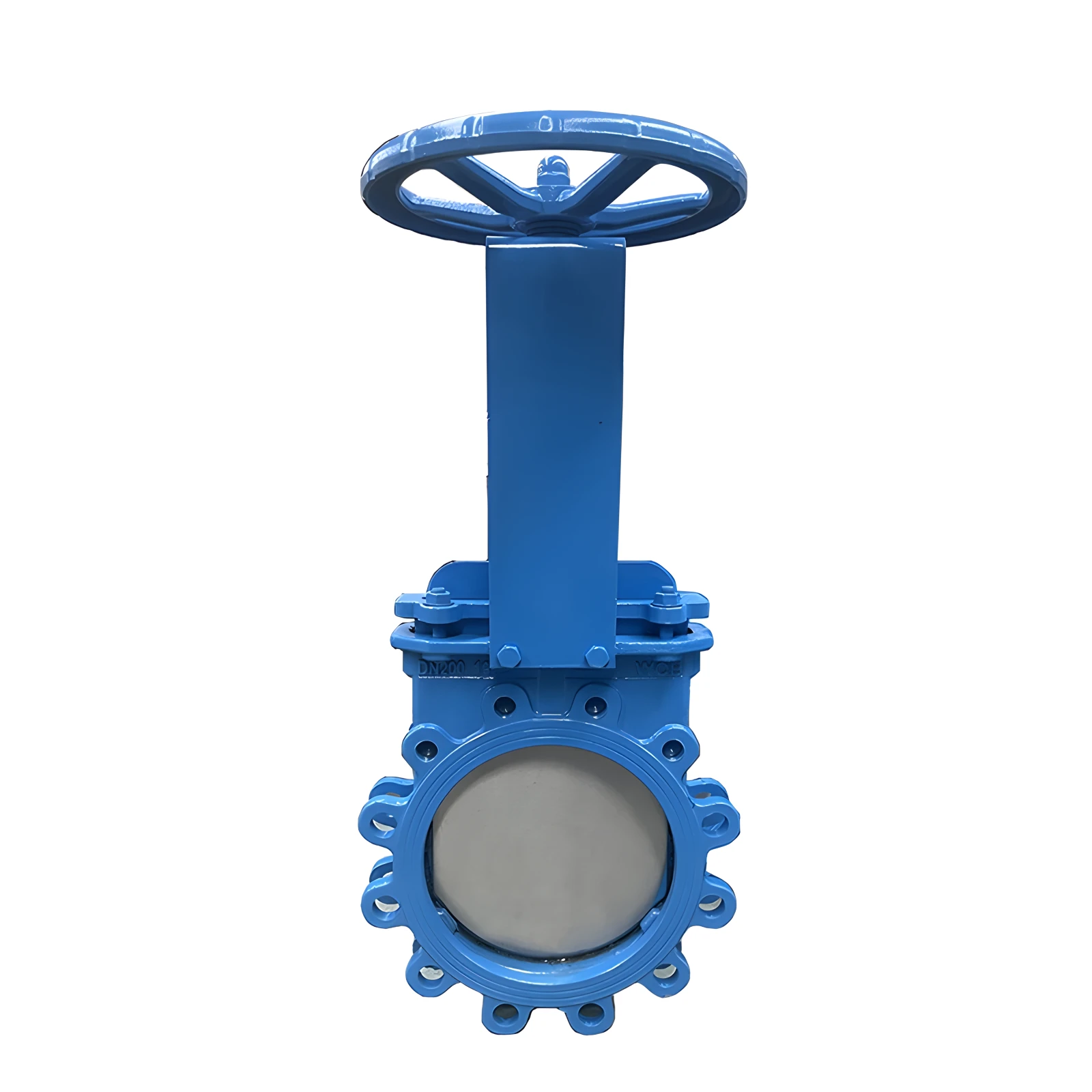
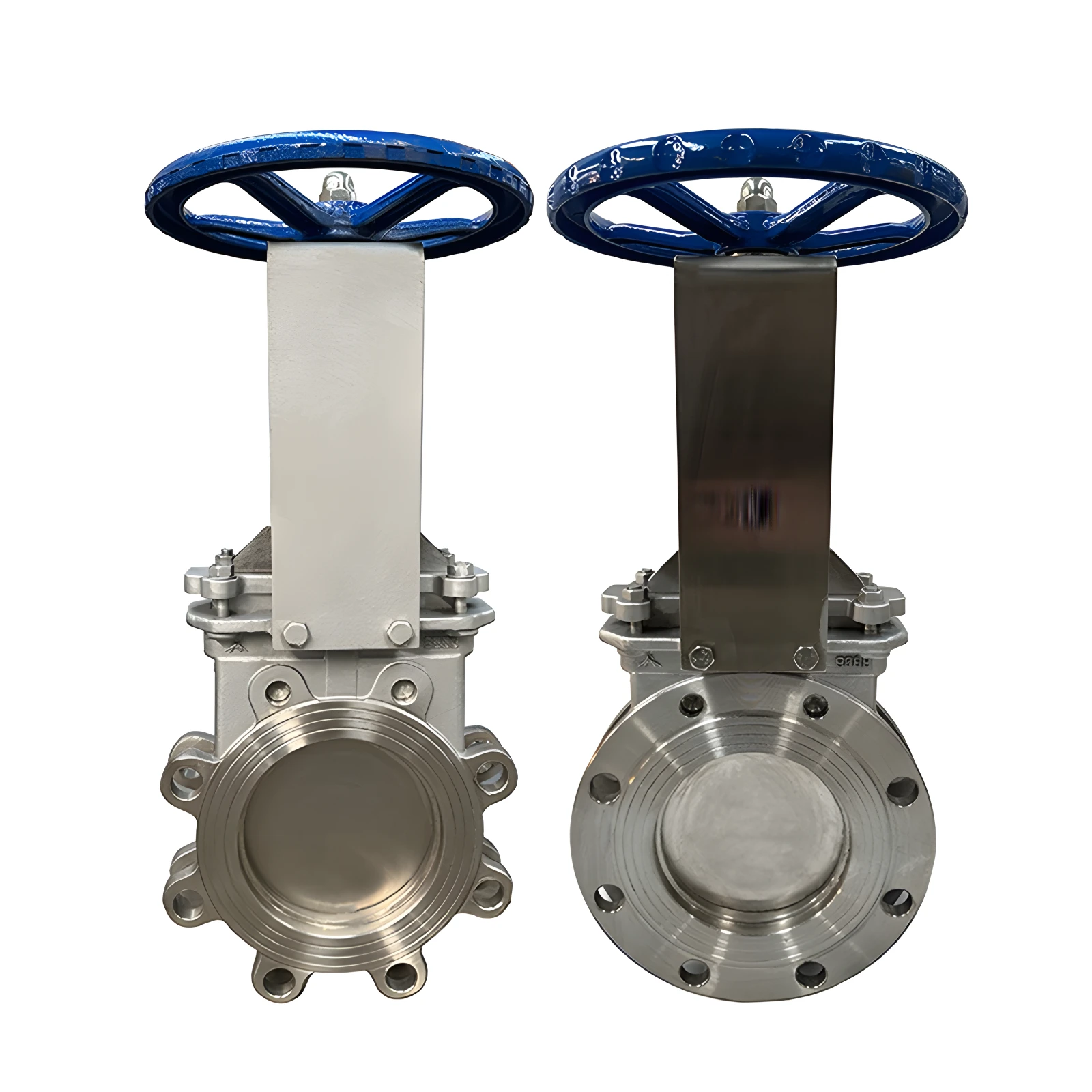